Spherical roller bearing
- Product features: Strong radial bearing capacity, can withstand two-way axial load;
Good impact resistance, suitable for vibration, impact conditions;
Has excellent aligning property, can adapt to the installation of wrong center, aligning angle can be more than 3°.
- Main areas: Papermaking machinery, reducer, railway vehicle axle, rolling mill gear box bearing seat, rolling mill roller, crusher, vibrating screen, printing machinery, woodworking machinery, various industrial reducer, etc.
Spherical roller bearing
Spherical roller bearings have the inner ring or double raceways, the outer ring of one spherical raceway and two row barrel rollers. The center of the spherical outer ring raceway and the center of the bearing is the same (see fig. 1. ), but the center line of the crossed inner ring raceways has an angle to the bearing center line, which can allow the bearing misalignment or the shaft-alignment without the influence from the housing misalignment or the shaft deflection. They can accommodate not only radial loads but also axial loads in two directions, suitable for those vibration and impact loaded applications.
HRB Spherical roller bearings can accommodate much heavy loads because they have a great number of long symmetrical rollers of large diameter. The modified form and excellent surface condition of the double raceways ensure these bearings of C and CA designs to have the lowest friction. Compared with conventional spherical roller bearings, these bearings are good at reducing operating temperature, enhancing heavily axial load carrying capacity or high speed ability.
HRB Spherical roller bearings are made with a cylindrical or tapered bore, for example, 240 and 241 series bearings with tapered bore of taper 1:30 (suffix K30), other ones with tapered bore of taper 1:12 (suffix K).
Design
C and EC designs
Such bearings of C and EC designs have symmetrical rollers retained by pressed steel cages which are rided by the inner ring. The EC design bearings are accompanied with enhanced rollers which improve load carrying capacity. The refined surface roughness of rollers and raceways improves roller guidance and reduces internal friction.
CA and ECA designs
Bearings of CA and ECA designs have symmetrical rollers and retaining ribs on the inner ring. One guide ring is placed between the two rows of rollers, centered by the inner ring. A machined solid cage of brass or steel is mated.
The CA and ECA bearings have the same refined surface roughness as that of the C design, but the ECA design bearings have enhanced rollers so as to increase load carrying capability.
Annular groove and lubricating holes
In order to facilitate lubrication, HRB basic design spherical roller bearings have one annular groove and three lubricating holes in the outer ring, except C design bearings of outside diameters less than 150mm or 180mm (subject to individual series respectively) and all 213 series bearings. C, CA, CE and ECA design bearings with suffix W33 have annular groove and lubricating holes in the outside ring.
Dimensions
The boundary dimensions of the bearings conform to ISO15-1981.
Angular misalignment
The unique design enables HRB spherical roller bearings to have an inherent self-aligning function which can compensate for angular misalignment of the inner and outer rings, values for allowable angular misalignment are given in the table when the inner ring is rotated under normal loads and working conditions.
Tolerances
Spherical roller bearings with cylindrical bore or tapered bore have normal tolerance, listed in the tolerance table in page 85.
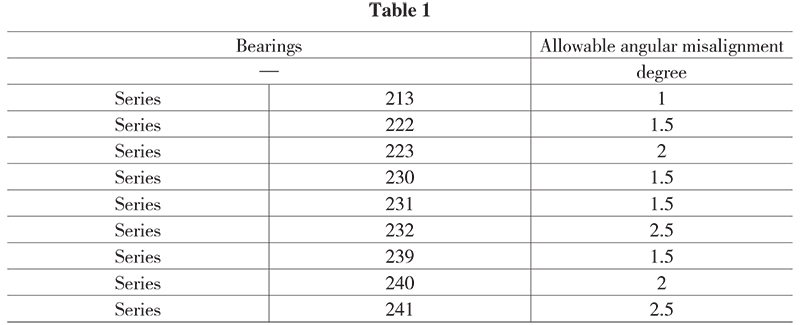
Internal clearance
HRB Spherical roller bearings have normal radial internal clearance. Most of them are supplied with C3 radial internal clearance, and some ones with C4 radial internal clearance. Some sizes of bearings are supplied with C2 radial internal clearance less than normal clearance. Values for various groups of clearance are shown in the tables on pages 67 ~68, in conformity with ISO5753. These values are valid for bearings having zero measuring load prior to mounting.
Heat treatment
HRB basic design spherical roller bearings are heat-treated in particular, so that they can work at operating temperatures upto +200℃,without any dimension change.
Minimum rolling bearing load
In order to attain to satisfactory running of bearings, including spherical roller bearings, there must be minimum required loads acting on them, or else during high speed running the mass forces of the balls and cage(s) and the inadequate lubricant resistance may generate a harmful sliding between the balls and raceways, easy to lead to bearing damage. The minimum required load is estimated from the following equation:
Frm = 0.02Cr
where
Frm: minimum radial load, N
Cr: basic dynamic load rating, N
In general, the bearing supporting weight adding the external forces always goes beyond the minimum required load. If not, an additional load has to be exerted, for example, increasing belt tension.
Equivalent dynamic bearing load
P = Fr + Y1Fa, for Fa/Fr≤e
P = 0.67Fr + Y2Fa, for Fa/Fr>e
Calculation factors e, Y1 and Y2 can be obtained from relevant bearing tables.
Equivalent static bearing load
P0 = Fr + Y0Fa
Calculation factors Y0 can be obtained from relevant bearing tables.
Catalog of HRB Spherical roller bearing